
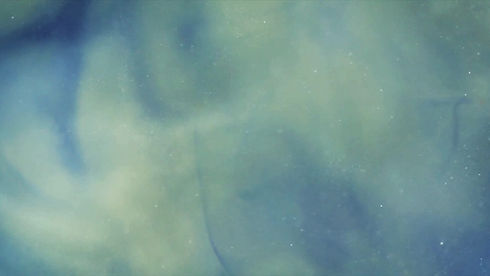
IBC Discharge Station
Automated emptying of intermediate bulk containers
Dec has developed economical solutions to discharge IBCs in a dust free and contained manner without the use of gravity. The IBC doesn’t need to be lifted above the equipment to be charged. It can be emptied by using the PTS Powder Transfer System® which is directly installed on top of the equipment to be filled such as a compactor, granulator or a tablet press thus removing the need of a second floor or IBC lifting column.
Due to the low speed transfer and dense phase operation, PTS guarantees no powder segregation or powder attrition during the transfer thus eliminating the risk of product separation typically occurring when charging chutes.
By a single discharge station multiple equipment can be charged decreasing the overall plant footprint and investment.
Dec offers various designs depending on the level of containment. The IBC will be installed on a discharge frame equipped with a docking system starting from a simple gasket solution for low containment to a butterfly split valve system for full containment requirements.
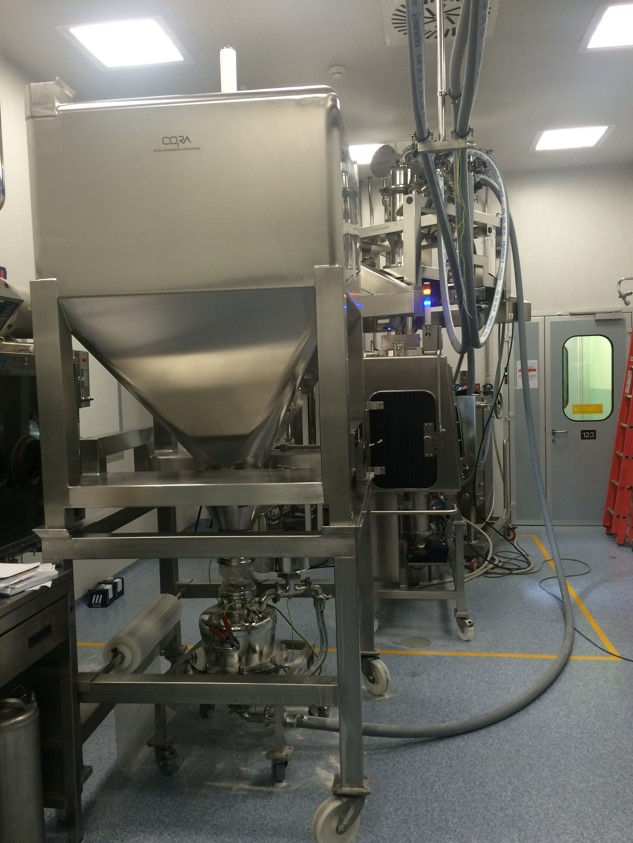


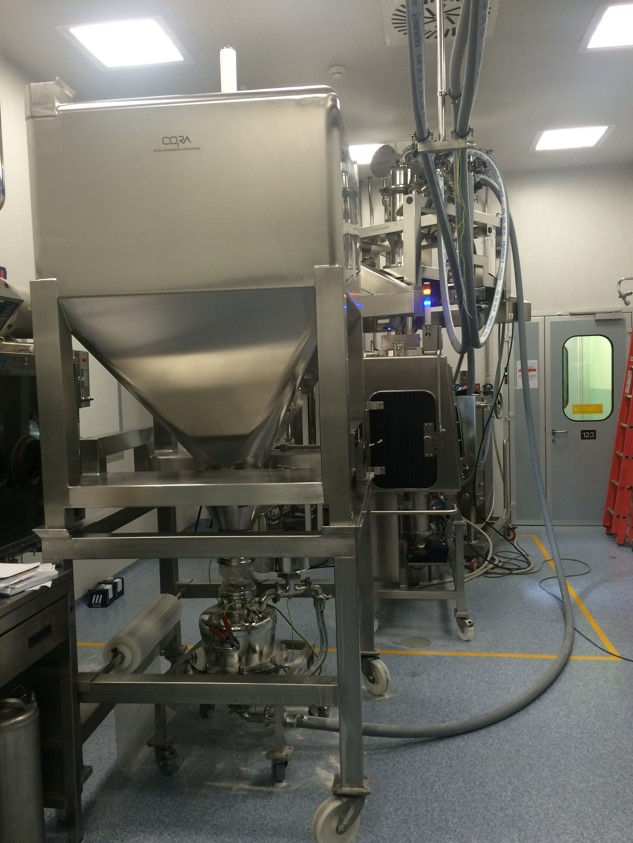
The station can be installed on load cells and include an additional vibration frame to facilitate t...
The station can be installed on load cells and include an additional vibration frame to facilitate the discharge in case of bridging materials.
The suction hopper connected to the station can be equipped with a delumper when agglomerated and lumpy products are involved. By integrating a discharge suction cone directly into the IBC, a docking station becomes needless . That way the IBC doesn’t need a bottom valve or a butterfly split valve but will be equipped with a simple shut-off valve or SafeDock Valve in case of higher contaiment needs onto which the suction shoe and the transfer hose are connected.
In order to save space and costs, Dec can provide a combined station for discharging IBCs and FIBCs.
The complete system can be cleaned in place and is suitable for operation in ATEX zone 1/21.